On Monday Airbus announced its 10,000th order with a firm contract from Virgin America for 60 A320s, including 30 A320neo aircraft. This is the first firm order for the A320 new engine option; therefore Virgin America becomes the launch customer for the A320neo. This formalizes and expands an initial commitment given at the Farnborough International Airshow in July 2010 with the inclusion of the A320neo as a new development in that deal. The 30 A320s will feature fuel-saving large wing tip devices called Sharklets. Virgin America has not yet announced its engine choice on the newly ordered A320s or the A320neo. Seating configuration on the aircraft will be the same as its existing A320 fleet (146-149 seats) in a two-class configuration.
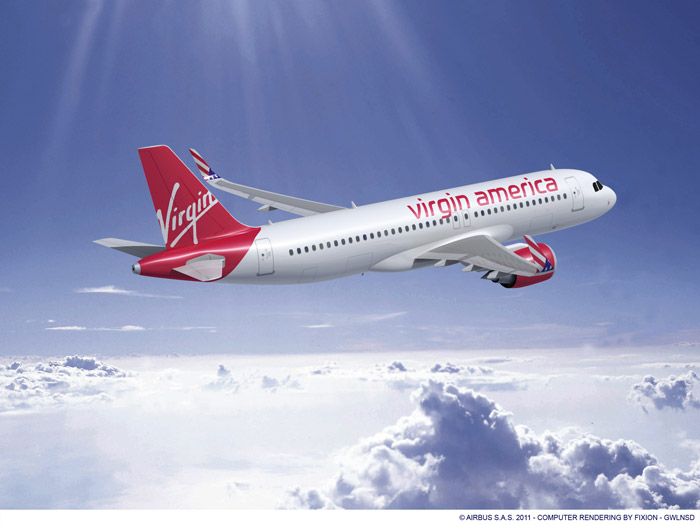
“At just three years old and at a time when many carriers are contracting, we’re pleased to be growing and bringing our award-winning service to new markets,†said Virgin America President and CEO David Cush. “We credit a great deal of our success to date to having the right aircraft. The low operating costs, cabin comfort and carbon-efficient design of our all-new Airbus A320 fleet has helped fuel our growth and success in the North American market – and we’re confident the A320neo will only build on that.â€
“We hit our 5000th order in August of 2004 – after more than 30 years. To achieve the 10,000th order just over six years later is a ringing endorsement of our product line,†said Tom Enders, Airbus President and CEO. “And it gives a strong boost to our new, eco-efficient A320neo when ‪Virgin America, one of our newest and trendiest customers, places the first firm order, for which we are extremely grateful.”
The A320neo responds to heightened customer environmental interest, offering a 15 percent reduction in fuel consumption. The option was launched in late 2010 for first deliveries in early 2016. Airlines have the choice between CFM International’s LEAP-X engine and Pratt & Whitney’s PurePower PW1100G engine. Each variant of the A320neo incorporates Sharklet wing tip devices. In addition to fuel savings, the A320neo will benefit from a double-digit reduction in NOx emissions, reduced engine noise, lower operating costs and up to 500 nautical miles more range or two metric tons more payload. The A319, A320 and A321 models on which the new engine option is offered will have 95 percent airframe commonality with the A320 Family, thus the A320neo will fit seamlessly into the existing Virgin America fleet.
Since the first Airbus aircraft went into service in 1974 with Air France, Airbus has seen sales of its aircraft grow steadily. By 1989, after its first 15 years in operation, Airbus had sold 1,000 aircraft. Less than half that time again, just seven years later in 1996, sales had risen to 2,000. Sales of Airbus aircraft had reached 3,000 in 1998, again cutting the time it took to sell another 1,000 planes by more than half. And by 2000 a total of 4,000 aircraft had been sold to the market.
Source: Airbus
Image: Airbus